Safety Above: 5 Uses of Fall Arrest Anchors in Window Cleaning
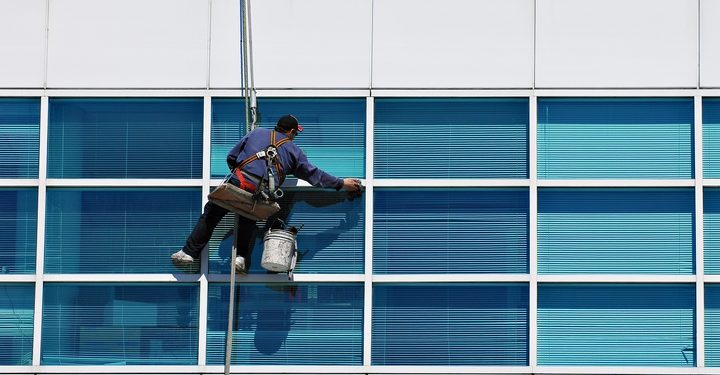
Regulations on the type of fall protection equipment used by building owners for window washing or window washing companies are tighter than before due to unsafe practices. Equipment such as Fall Arrest Anchors have to be tested, certified, maintained and approved before applied at the project site. An important step is to design the system to meet applicable codes and standards. To achieve this, organizations apply careful planning to develop a suspended maintenance system that is both safe and compliant.
More importantly, this equipment should be suited for the building as each one has unique conditions and access points affecting the way the window cleaners perform their duties. This equipment should be capable of supporting a certain capacity in any direction or angle.
Building owners are responsible for ensuring that they hire a company with the right fall protection equipment that meet their building specifications. Here are the reasons:
1. Keep employees safe
Safety is the most important reason for installing the correct safety system as accidents cause pain and sadness. Employees will feel safe and secure when the fall protection equipment has been certified and approved. It is the employer’s and the building owner’s responsibility to keep the employee safe from dangerous falls at the workplace. They have to provide working conditions free of unknown danger. When choosing a provider, make sure the fall arrest anchors are safe and exceed both local and federal legislative requirements.
2. Comply with regulations
Many health and safety regulation authorities have established rigid safety standards for employers to meet. There are standards that apply for difference industries, applications, workplace environments, equipment use and job functions. These regulation authorities expect all organizations to take safety seriously. Workplaces should be hazard free. Systems in place should prevent falls from any work surface including elevated locations. Additionally, equipment design and manufacturing should meet standards and codes.
3. Prevent liability
Falls are common workplace safety violation resulting in fatal injuries and costly worker compensation costs. This can result in lawsuits and other unfavorable circumstances. No employer or building owner wants to face liabilities.
This is the main reason for organizations to be proactive in ensuring they meet regulations and standards, train employees, test and certify equipment, and implement systems that prevent fatal accidents. Many manufacturing providers of fall protection equipment work with cleaning organizations to determine the right set of equipment for various types of buildings.
4. Enhance employee performance
Prevent falls by making sure employees understand how the equipment works including the proper set-up and safe use of the equipment. The window washing company or equipment provider should ensure that the employee is fully trained to use the equipment. The training should cover the potential hazards and the use of appropriate equipment and systems. When employees feel safe and are trained on the equipment, they are more productive. They trust that their employer has their safety in mind at all times.
5. Ensure business success
The window washing company, the building owner and fall protection equipment provider can increase profitability when there are no litigations against their organization. A company with no history of fatal accidents and with a reputation of meeting or exceeding regulations is likely to attract customers and do well in business.
Organizations have to be proactive in their actions to prevent fatal accidents, keep employees safe and protect their company reputation. You can achieve this by hiring a company that designs fall arrest anchors that are strong, approved by regulation authorities and tested for safety, making subsequent steps of implementation and training employees much simpler. The design also implements practical and convenient methods used by the employee.